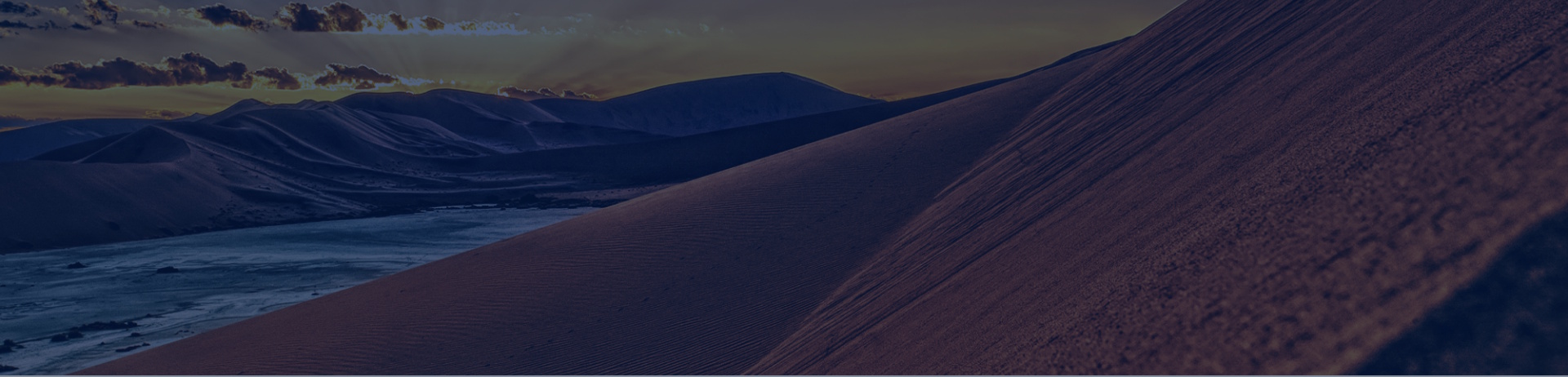
Field Manager - Oil & Gas Sector
Minimum Qualifications:
- Bachelor’s degree in petroleum, mechanical or Chemical Engineering from a recognized university.
Minimum Qualifications:
- Minimum of 15 years of experience in Oil & Gas projects.
- Extensive experience in multidisciplinary EPIC projects within the Oil & Gas sector (EPIC projects including EPF, CPF and GTP).
- 5 to 10 years of prior field operation, supply chain management, on-site operations, or related experience.
Reports to the Country Manager in the Country Head Office. The Field Manager is directly responsible for the day-to-day operation of the wells and facilities including sales transfers to the pipeline. This includes optimisation of production, control of operating costs, safety of field personnel, integrity of Company assets and the maintenance of environmental standards. These responsibilities will be carried out in accordance with Company commercial, production, safety and environmental goals.
Key Responsibilities:
- Carry out the activities of Company and subsidiary companies in accordance with company policies and procedures.
- Operate the facilities in a safe and prudent manner so as to minimize the risk to personnel, company property and the environment.
- Endeavor to maximize the production levels at the Field at all times.
- Endeavour to optimize produced water treatment, discharge and water injection systems at all times.
- Ensure that all company safety policies, programs, and procedures are followed at all times.
- Receive and Quality Check Daily production & injection data on a well by well basis. Prepare all field production reports as required.
- Strive to maintain operating expenditures at or below budget.
- Monitor well and equipment performance on a daily basis to ensure optimum operating conditions are maintained.
- Plan and execute rig and pumping wellwork jobs including pressure and other data gathering runs.
- Ensure that all spare materials, downhole pumps, rods, field chemicals, fuels, lubricants, lab supplies, etc are maintained at adequate levels to minimise downtime.
- Anticipate field and well downtime scenarios and plan for power outages to maintain maximum oil production.•
- Ensure all field operating and maintenance procedures are closely followed. This will include sales transfers, well testing, product quality testing, preventative maintenance, security, environmental.
- Liaise with Custody Transfer Operator on a regular basis in relation to oil sales technical compliance.
- Report immediately to management all safety issues, equipment malfunctions, and changes in well operating conditions, that could potentially interfere with the safety of the onsite personnel and/or the oil production volumes.
- Recommend to management any changes/modifications to improve the field operation.
- Manage the affairs of the Accommodation Camp facilities so as to ensure all Company functions are adequately equipped.
- Project and maintain a positive work environment for all the field personnel.
- Report to management immediately all significant issues that may arise from time-to-time regarding security and local personnel
- Perform tasks and duties as directed by the Operations and Country Manager.
Delegation of Authority:
The Field Manager can delegate work activities to the designated field operations Senior Operator positions and the wellsite Petroleum Engineer. The position works closely with the field Safety Officer, Field operations and Maintenance Personnel, Contract well service personnel and the Company Country Office staff.
Health Safety and Environmental:
- Read, Implement and Improve all E&P HSE Policies and Procedures
- Strive to achieve zero LTIs, Oil Spills and other HSE key objectives
- Hold regular Safety Meetings and document attendance
- Ensure Emergency Response Procedure is up to date, relevant and emergency response drills performed.
- Ensure Emergency Response Team is in place in Field and Company Country Head Office
- Ensure Emergency Response Communications are working
- Implement Permit to Work System
- Participate in HSE Inspections with Safety Officer
- Participate in Tool Box Talks with Safety Officer
- Respond to Oil Spills and ensure correct Reporting and follow-up
- Familiarise with Routine HSE Reporting and Inspections
- Participate in Incident Response and Reporting with Field Safety Officer
- Ensure Contractor Compliance with Company Policy and Procedures
- Familiarise with Environmental Monitoring routines for Air, Water etc.
- Ensure Good Housekeeping is in place and Waste Management
- Prepare and Implement Waste Management Plan with HSE Department
- Implement remedial activities based on HSE NCRs
- Issue NCRs to Contractors and ensure follow up
- First Aid Training and response
Production Operations and Reporting:
- Ensure Daily Production Report is accurate and sent out by 8:00 am
- Perform decision making and actions on Active Well Optimisation
- Ensure accurate Gauging and Well Testing of all wells according to Standard Operating Procedures
- Plan Oil Sales activities and liaise with receiving company for timing - be present for sales verification
- Supervise key operations on wells, operations and civil/Construction activities
- Supervise Well Stimulation Activities in compliance with approved Workover Programmes
- Supervise Well Rig Workover Activities in compliance with approved Workover Programmes
- Respond to well and plant downtime incidents to optimise safe production
- Ensure daily fluid level priorities are performed by operations personnel Familiarise with Echometer Well Analyzer Equipment and perform Well and Pump Diagnostics
- Perform ESP Optimisation / Pump Jack Balancing with operations personnel
- Ensure Back-up power generation is in place and operational – testing frequently
- Review Monthly Field Factor (Sales vs Meters) and investigate any drift from historical figures
- Prepare and update Standard Operating Procedures and ensure operations personnel are trained
- Implement Water Injection Allocation as per Petroleum Engineer issued guidelines
- Devise Field Annual Key Performance Indicators for Safety, Production, Uptime, Water Injection, Housekeeping, Oil Spills, etc.
Production Optimization:
- Perform Well by Well optimization for maximum oil production
- Review well performance for production problems including sand, water, scale, wax etc
- Optimise oil production surface facilities and well testing procedures
- Perform pump diagnostics on under-performing wells and recommend workovers
- Make suggestions over alternative artificial lift options based on well performance
- Discuss workover activities with Country Manager/Sr Petroleum Engineer
- Prepare and Supervise Production Enhancement workovers including well stimulations
- Review inactive wells for potential re-activation
- Ensure Water Injection activities are performed
- Ensure injection water quality is monitored for salinity, turbidity etc.
- Optimise water injection surface facilities
- Optimise Produced water volumes and treatment for Re-injection
- Review Water Injection responses at offset wells
Maintenance Optimization:
- Identify all Field Equipment and establish Equipment Criticality
- Ensure Equipment Maintenance Procedures are available and vendors for spares are known
- Respond to Equipment Downtime Incidents
- Develop and Implement Equipment Periodic Maintenance Routines
- Perform Corrosion Monitoring routines and recommend actions
- Ensure adequate spares for routine and breakdown maintenance activities
- Discuss critical equipment redundancy with Country Manager
Field Inventory:
- Maintain a database of field equipment including Downhole Pumps and Pumpjacks
- Identify Minimum and Maximum Levels of Field Equipment and consumables
- Order new items to ensure minimum levels are maintained
- Sign off Goods Received Notices for delivered items and check condition
- Make recommendations on new field equipment, tools, facilities
Contractor Management:
- Ensure all in-field Contractor Personnel report to you and movements are monitored
- Ensure Contractor Compliance with HSE Policy and Procedures
- Provide Daily and Job Specific Work Direction to Contractors
- Implement Permit to Work Procedure
- Obtain quotations for specific Scopes of Work in conjunction with Country Manager
- Sign off on Job Tickets - ensure information is coded for accounts purposes
- Provide Feed-back on Contractor Management to Country Manager
Budget Control:
- Own and Control Budget Line items relating to:
- Well Maintenance
- Downhole Pump Repairs, Spares
- Water and Oil Trucking
- Civil Work
- Electrical Work
- Pipefitting Work
- Camp Management
- Vehicles and Fuel
- Electricity Usage
- Production Consumables
- Maintenance Activities, Spares and Consumables
- Ensure HSE Own and Control Budget Line Items relating to:
- HSE Equipment
- Environmental Testing
- HSE Training
- Company PPE
- Waste Management
Capital Project Implementation:
- Provide Field Supervision of Capital Projects Implementation
- Potential Capital Project Listing
- Water Injection Expansion
- New Development Well Commissioning
- Mobile Well Stimulation Package
- Mobile Well Testing Unit
- Field Artificial Lift / Insert Pump Maintenance Workshop
- Field Accommodation Expansion
- Vertical Pump Testing Facility
- Company owned Workover Rig Commissioning
- Drilling – Well Deepenings
- Perforation – New and Re-perf programs
- Field Laboratory
- Chemical and Lube Oil Storage
- Field Warehouse
Personnel Management:
- Provide Daily work direction to Field workforce
- Ensure correct level of coverage and supervision for field activities
- Perform annual performance reviews
- Participate in Recruitment Process
- Ensure night shift coverage is adequate
- Ensure compliance with Company HR Policies and Procedures
- Make recommendations on Promotions, Performance Bonusses, Recruitment, Re-assignments
Stay Up to Date
Connect with us on LinkedIn and Twitter